SQCDP: the visual management tool to improve daily production processes
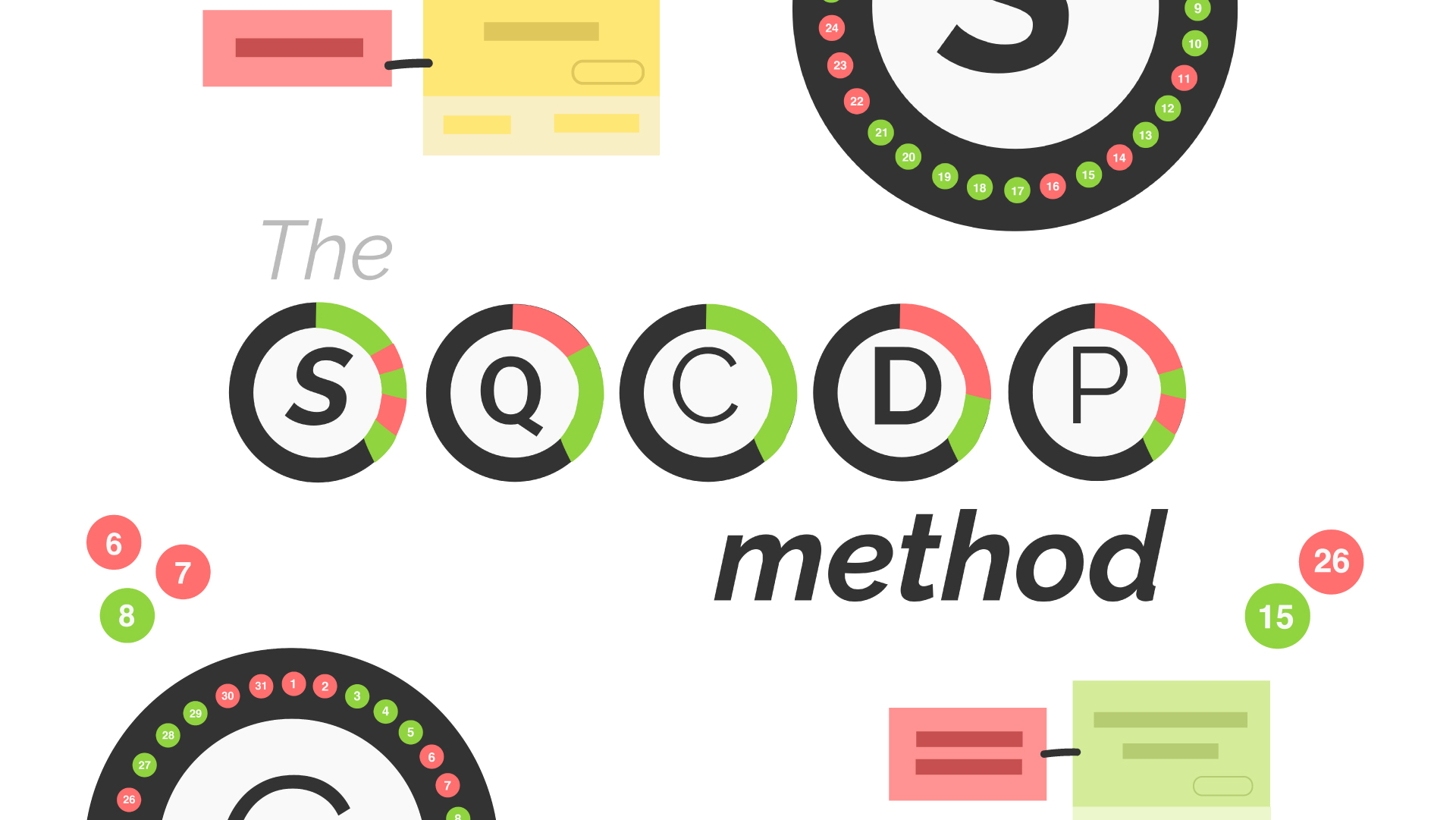
The SQCDP method
Whatever the industrial process, production performance is key. To meet their objectives, the teams need to rely on straightforward and detailed dashboards with a list of incidents and appropriate solutions. The SQCDP method is one of the most efficient solutions. This visual management tool is widespread among production units as it promotes continuous improvement. On a daily basis, team members can refer to this ready-to-use template to monitor and improve key performance indicators in a simple and effective way.
What’s the SQCDP method all about?
A visual management tool that promotes continuous improvement
The acronym SQCDP stands for Safety, Quality, Cost, Delivery and People. This visual management tool was initially used in the aviation industry, before reaching out to many different business areas.
Its very simple principle helps monitor and improve the key performance indicators of a production process, over the course of one month. It’s a collaborative dashboard used to ensure sustainable production unit performance at the required level.
This method is designed as a dashboard, or more specifically, five dashboards for each of the indicators of the SQCDP acronym.
- S for safety: covers accidents, injuries and protocol enforcement and implementation;
- Q for quality: covers production excellence levels and customer satisfaction;
- C for cost: covers cost control and resource optimization;
- D for delivery: covers workflow and time management, delivery and supply chain optimization;
- P for people: covers holidays and leave, overtime, human resources management.
A visual tool for the daily team meeting
The team can meet up daily on the production unit premises to review the previous day’s five KPIs.
Team members use the first space to color the corresponding box for the day, according to performance:
- Green if the day went smoothly, without any significant glitches;
- Red, on the other hand, if any incidents occurred during the day.
The team can decide the criteria for each KPI beforehand and determine the level of severity required for the box to be colored in red.
As the month progresses, an overall pattern emerges and the procedures and behaviors can be fine-tuned and improved to achieve the best possible performance level.
The second space is used to note down any incidents and the remedial action required. It can be populated at any time to provide real time information.
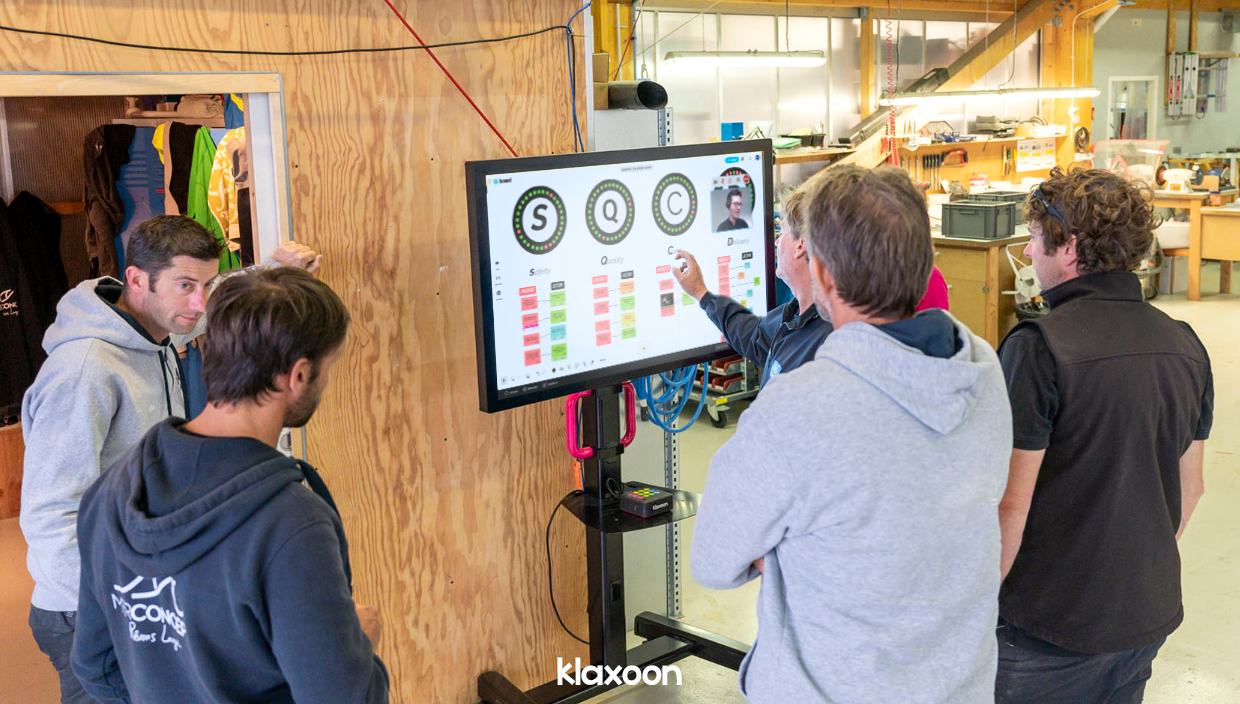
Why apply the SQCDP method with Klaxoon?
The benefits of SQCDP
With its visual dimension, the SQCDP is a very useful source of information for your teams. On a daily basis, you can use it to report incidents and the actions to be carried out. As the month progresses, you can monitor your activity and measure overall performance trends. It’s the ideal dashboard to improve a manufacturing or production process.
It’s a simple method, easily applied to the daily work routine.
Two key reasons for using Klaxoon’s Board for your SQCDP
All team members can take part, without any constraints in terms of location and time
Board is a digital whiteboard with unlimited communication possibilities, where ideas (text, image, video, document, link, etc.) can be easily shared as colored stickers for a highly visual effect. With its built-in videoconferencing tool, Live, all the team members can share ideas in real-time, in person and/or remotely.
Creating an SQCDP is a collaborative process which involves all the team members working on the production line (operators, logistics officers, quality managers, foremen, etc.). Board is therefore the ideal interactive solution for effective group communication!
People can even contribute in asynchronous mode. If a team member has missed the daily meeting, they can easily check whether the day was colored in green or red and catch up with any information available on the Board. Likewise, if the teams rotate between night and day shifts, they can pass on the information at the end of their shift.
Everyone can choose to communicate in the way that best suits them
With Board, you can post ideas as text, video or photo. It is particularly useful for information feedback. One image speaks volumes. A photo or video of a faulty machine or a product defect can be much clearer than a long written explanation.
This will make your SQCDP more visual and easier to understand for all the team members!
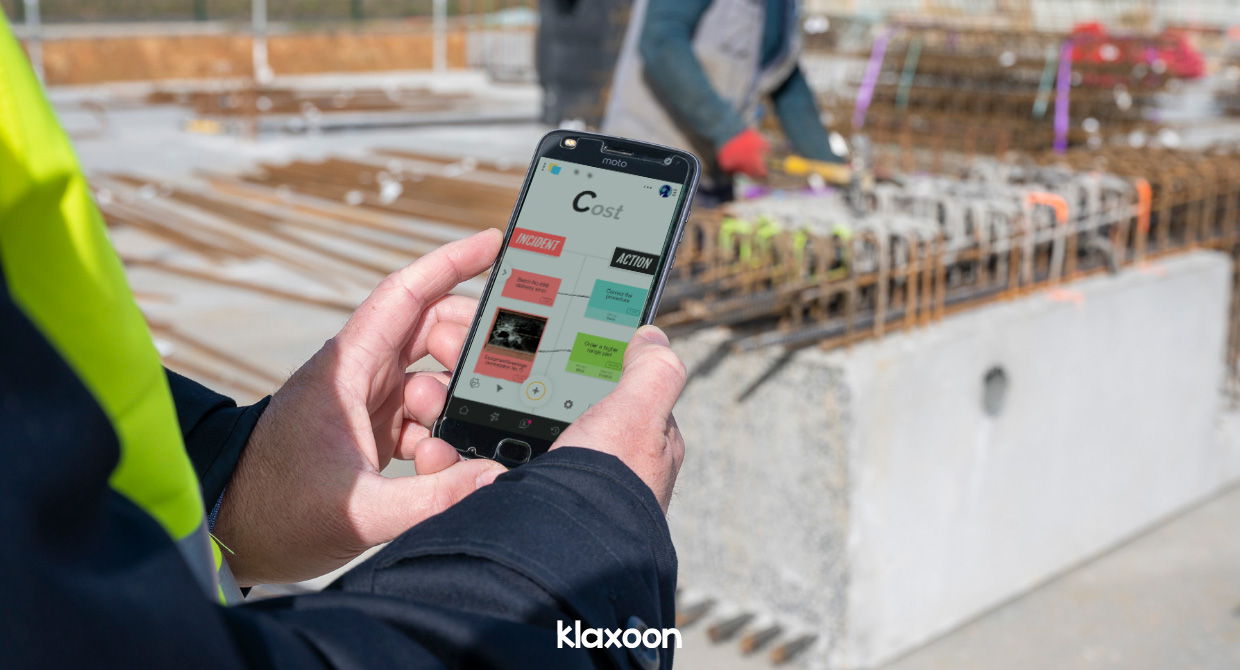
How to create your SQCDP on Board
This ready-to-use template, available in Klaxoon’s template library, will help you apply the SQCDP method to your procedures as a team.
Notify all useful information
In the table, each idea relates to one incident or action to be carried out. As soon as you identify a problem, report it in an idea. A photo, video or short description...you decide. Apply the color corresponding to your idea (red for an incident) and assign the relevant category (safety, quality, cost, delivery or people).
Enter the action to be carried out to remedy the incident in a different idea. Use the connectors to link ideas together and clearly associate particular incidents with the corresponding actions to be carried out.
Make this a routine when you start work and whenever necessary, as Board is available on your smartphone.
As a team, take stock of the previous day
During your daily team meeting, review any incidents and determine whether or not there was an incident during the day. Then color the day in red or green, accordingly.
As the month progresses, analyze the overall indicator trends and as a group, take the decisions required to improve your industrial process. Using Board’s predetermined color code, notify the progress of each action: yellow if the action is pending; blue if the action is in progress; green if the action is completed; and orange if the action is on standby.
Finally, make sure that the solutions to the problems effectively improve your procedures.
Write a report
At the end of each month, before starting a new Board SQCDP, review the past month, analyzing the incidents reported and completed actions. Take all the necessary measures to continue improving month after month and achieve your quality objectives.
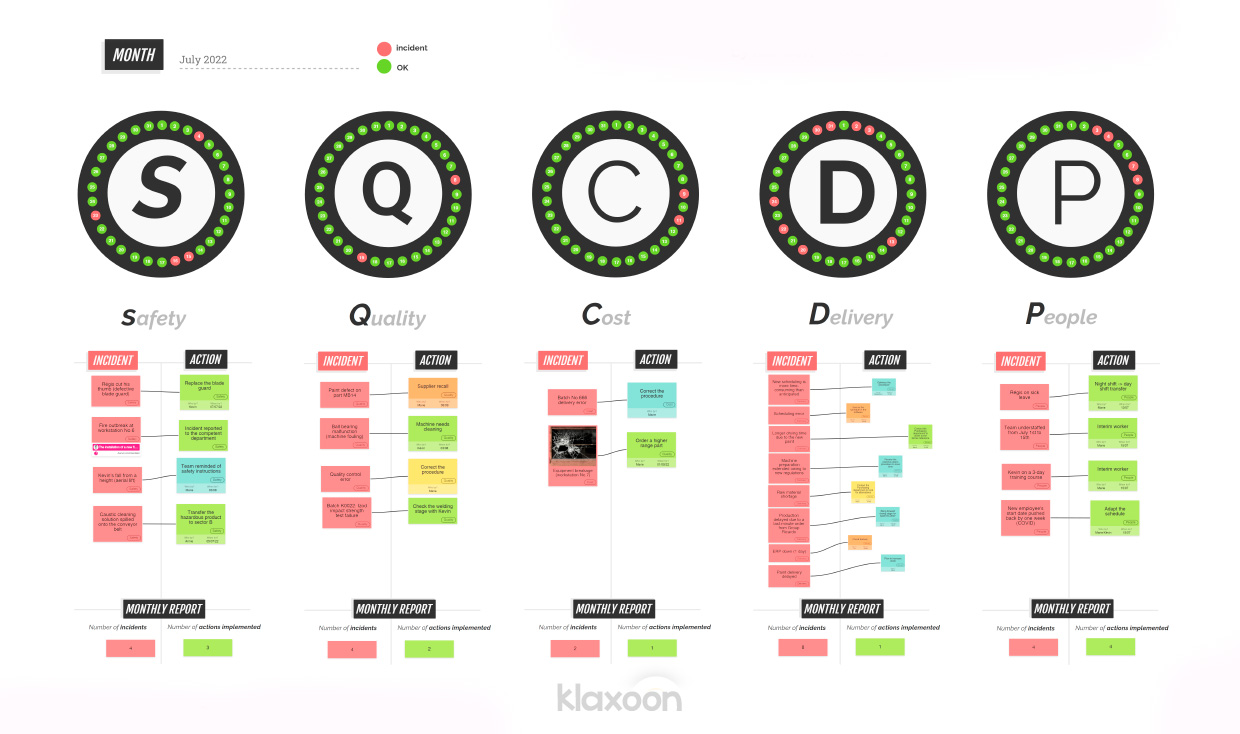
To develop the SQCDP dashboard approach
The SQCDP method, by identifying issues and finding the best solutions, is perfectly suited to a Lean Manufacturing approach. There are many other ways of implementing Lean Management, such as the PDCA cycle for example. This method helps you identify your issues and implement solutions for continuous improvement.
And to take things a step further, find out how Rémy uses Board to improve the visitor experience in one of France's best known amusement parks, using information feedback and real time processing.
You too can adopt Klaxoon!
With Templates, innovate in the management of your projects, represent them visually and move forward as a team in a synchronized manner