The A3 report: Lean Management, a problem-solving solution
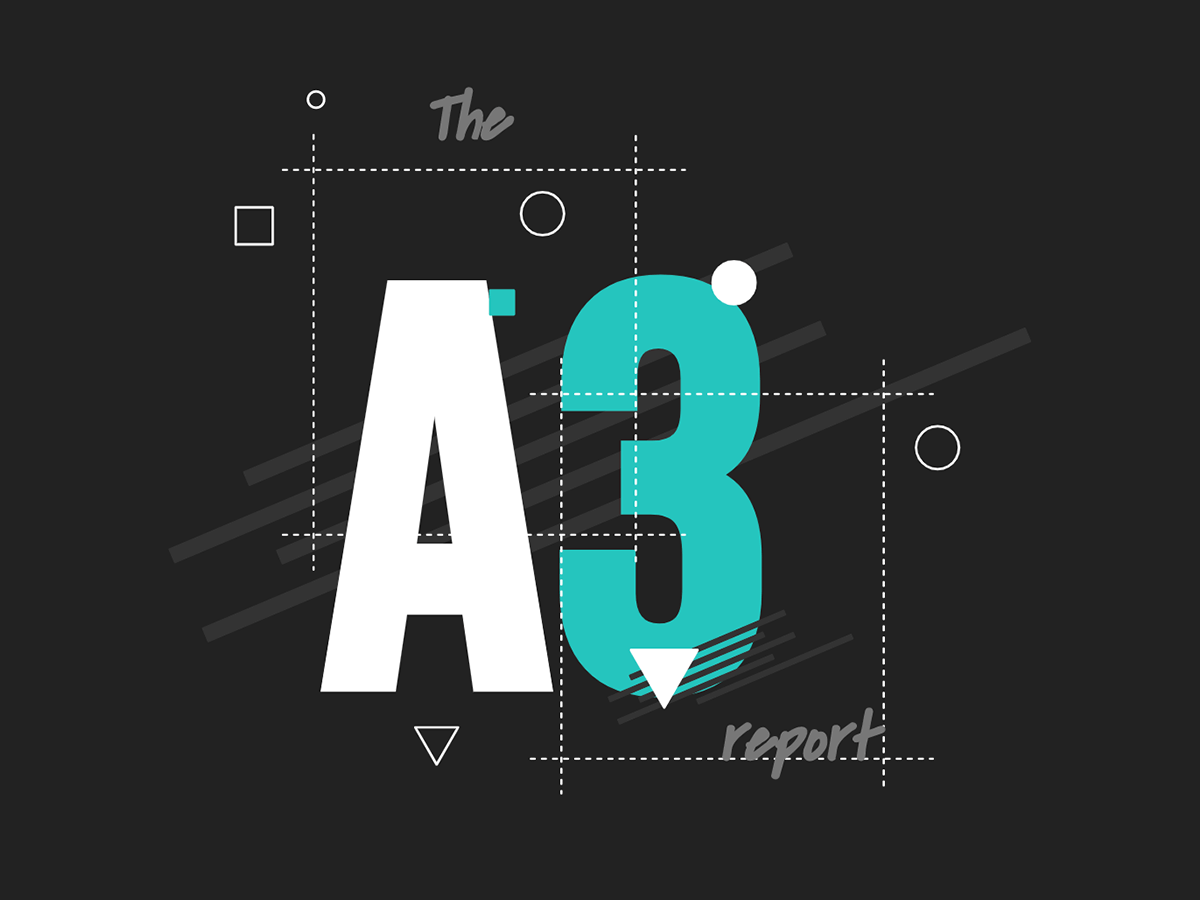
The A3 report
If the term “A3” brings back painful memories of the photocopying machine playing up as you’re running late for a meeting, where you’re giving a presentation of a major project, don’t worry, this article is not about office equipment.
The A3 report is part of the Lean Management methodology. Derived from Toyota’s production system, it organizes work processes and aims to improve efficiency within the company, in particular in terms of quality and profitability.
Sorry, but we do have to briefly mention office equipment at this point...At the time when the A3 report was created, back in the 70s, the fax machine was one of the main means of communication. Those machines accepted sheets of paper up to the A3 format, hence the name of the report.
Although fax machines are now a thing of the past, the method itself is still very much in use! With Klaxoon’s Board Hybrid, no need for paper, but the benefits of the A3 report are still there, i.e. well organized and to-the-point problem-solving processes!
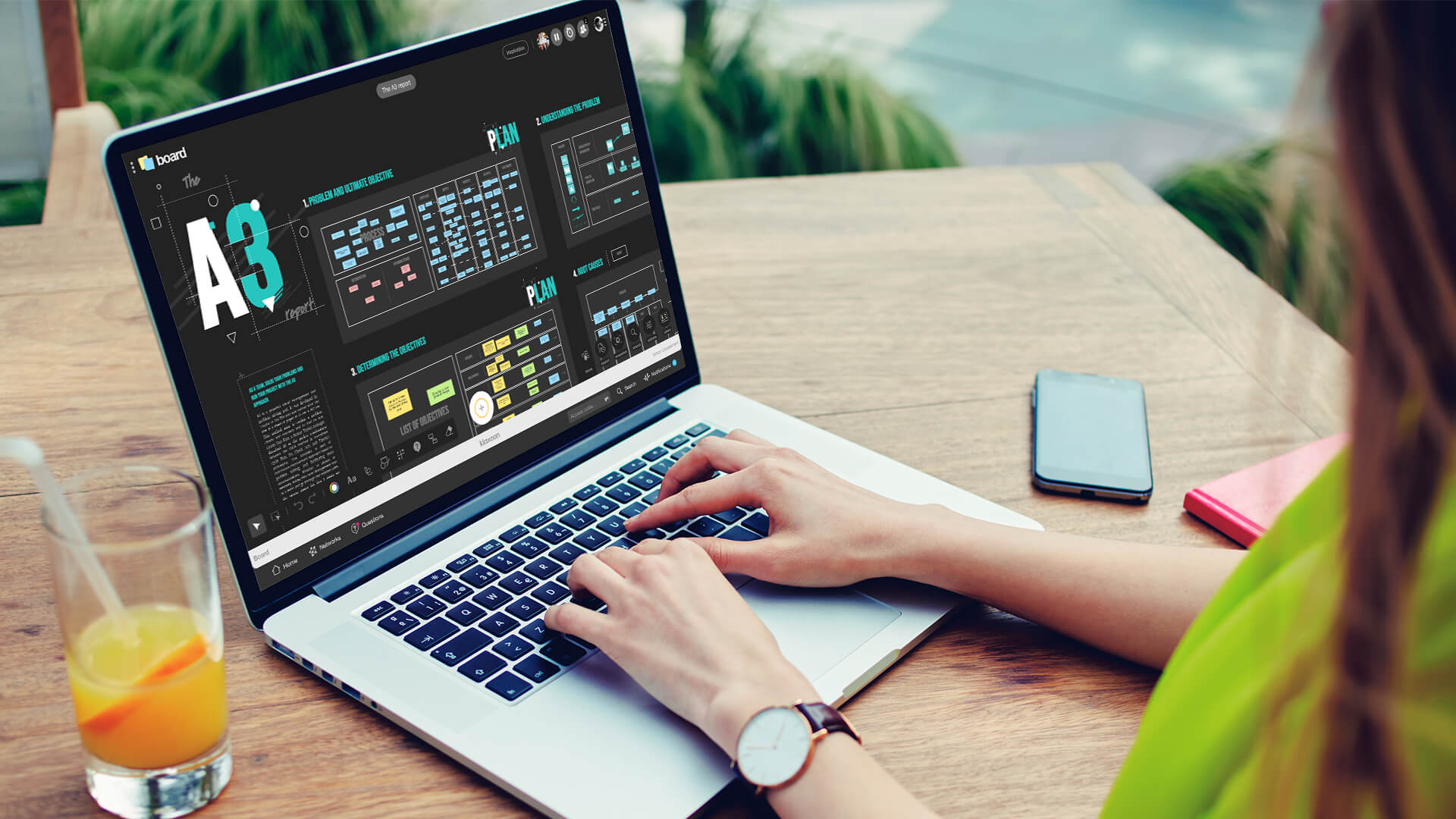
What is an A3 report?
A 42 x 29.7 cm sheet of paper is not that big when it comes to reporting, analyzing and solving a problem. But it means you have to be to the point, know how to prioritize and be concise.
The A3 report covers a sequence of 8 successive stages. They are part of the Deming wheel, with a 4-phase cycle that is part of a continuous improvement approach: Plan-Do-Check-Act (PDCA).
An A3 report is a team process, not an individual one. It’s a highly visual tool, with a standardized framework that promotes analytical and synthetic skills, where everyone focuses on key elements. It is a clear reference point for the team, for each new project.
Commonly used as a problem-solving tool, the A3 report can also have other uses, such as making suggestions and demonstrating their relevance.
How does an A3 report work?
Designed according to a PDCA cycle (a.k.a Deming wheel), the A3 report follows a specific protocol, that aims to:
- Understand the problem and find its root cause
- Implement the best solution
- Check that the retained solution is in line with the expected outcome
- Take any necessary action
This cycle encompasses 8 phases, which must be completed as a team, and repeated until the end goal is met.
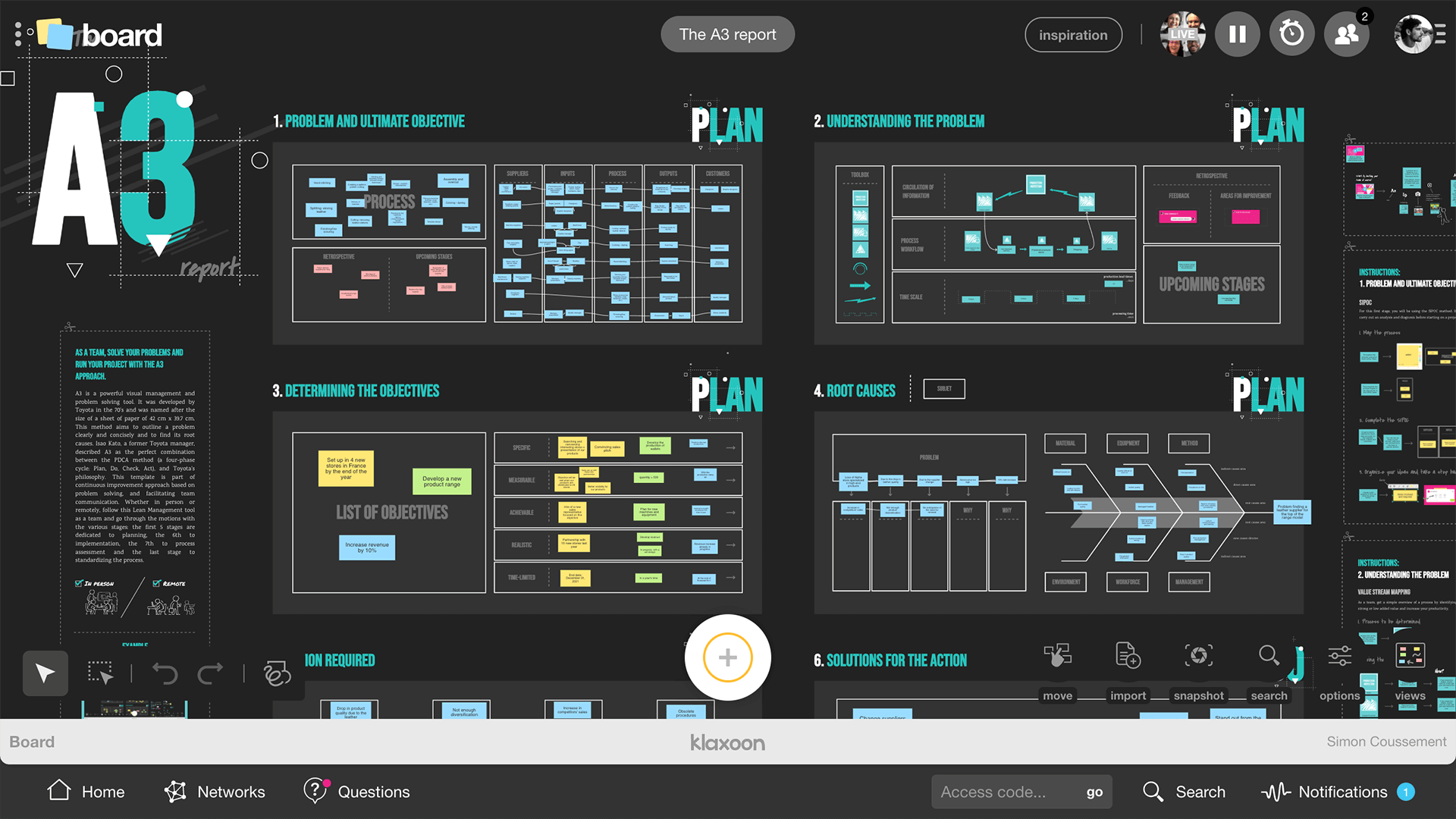
Stages 1 to 5: PLAN
This phase involves preparing the work, from the factual description of the problem, up to the tasks to be done, as well as setting goals.
- Stage 1: Describe the problem and set the end goal.
Start by using the SIPOC method, ideal for a detailed description of a process. The acronym SIPOC stands for Suppliers, Inputs, Process, Outputs, and Customers. Analyzing these 5 elements highlights the ins and outs of a process, and helps determine the core of the problem and its consequences. You naturally shed the light on the end goal, to make sure that the problem will not happen again in future.
- Stage 2: Understand the problem.
Nothing better than a Value Stream Map (VSM) to easily view the production chain, from the supplier to the customer. By listing all the actions involved in the process, you highlight those with high added value, and those with low added value. This provides you with a great overview of the situation, helping you to fully understand the problem.
- Stage 3: Set the goals.
Think SMART! This acronym refers to the 5 adjectives that qualify your goals: Specific, Measurable, Achievable, Relevant, Time bound. By following this principle, you will be sure to set your goals properly, so that they are understood and achievable by all.
- Stage 4: Identify the root causes.
The detective work begins! It’s time to investigate the root causes of the problem, the true reasons why the goal was not met. You have two tools on hand.
The “5 whys” method, which aims to ask the question “why” until you get to the root cause of the problem.
Another option is the Ishikawa (or Fishbone) method and its causes and effects diagram. The problem necessarily results from factors known as the 5Ms: Materials, Machines, Methods, Manpower, Medium. By looking at each one, you’ll be able to identify the root causes.
- Stage 5: Take the necessary actions.
Relying on the root causes you identified earlier, determine the solutions to be implemented.
Stage 6: DO (or Deploy)
This phase involves implementing the solutions identified in stage 5. You must pick the most relevant solutions and detail their implementation in an action plan (what, who, by when).
Stage 7: CHECK
This phase aims to make sure that the action plan has been executed and that each action has produced the expected outcome. To make sure of this, identify the positive and negative points of the actions undertaken.
Stage 8: ACT
This is the final phase in the PDCA cycle and it serves as a final assessment for the team. The aim is to standardize a functional process, so assess the relevance of the actions undertaken and prioritize them according to relevance (those to be retained, discarded or tested).
Why carry out an A3 report with Klaxoon’s Board?
Board Hybrid is a collaborative tool developed by Klaxoon to improve teamwork. It comes in the form of an unlimited digital whiteboard. Admittedly, within the context of A3 reports, which specifically require organizing information within a limited format, this is not an essential element. However, Board features many other strong points that you’ll find very useful…
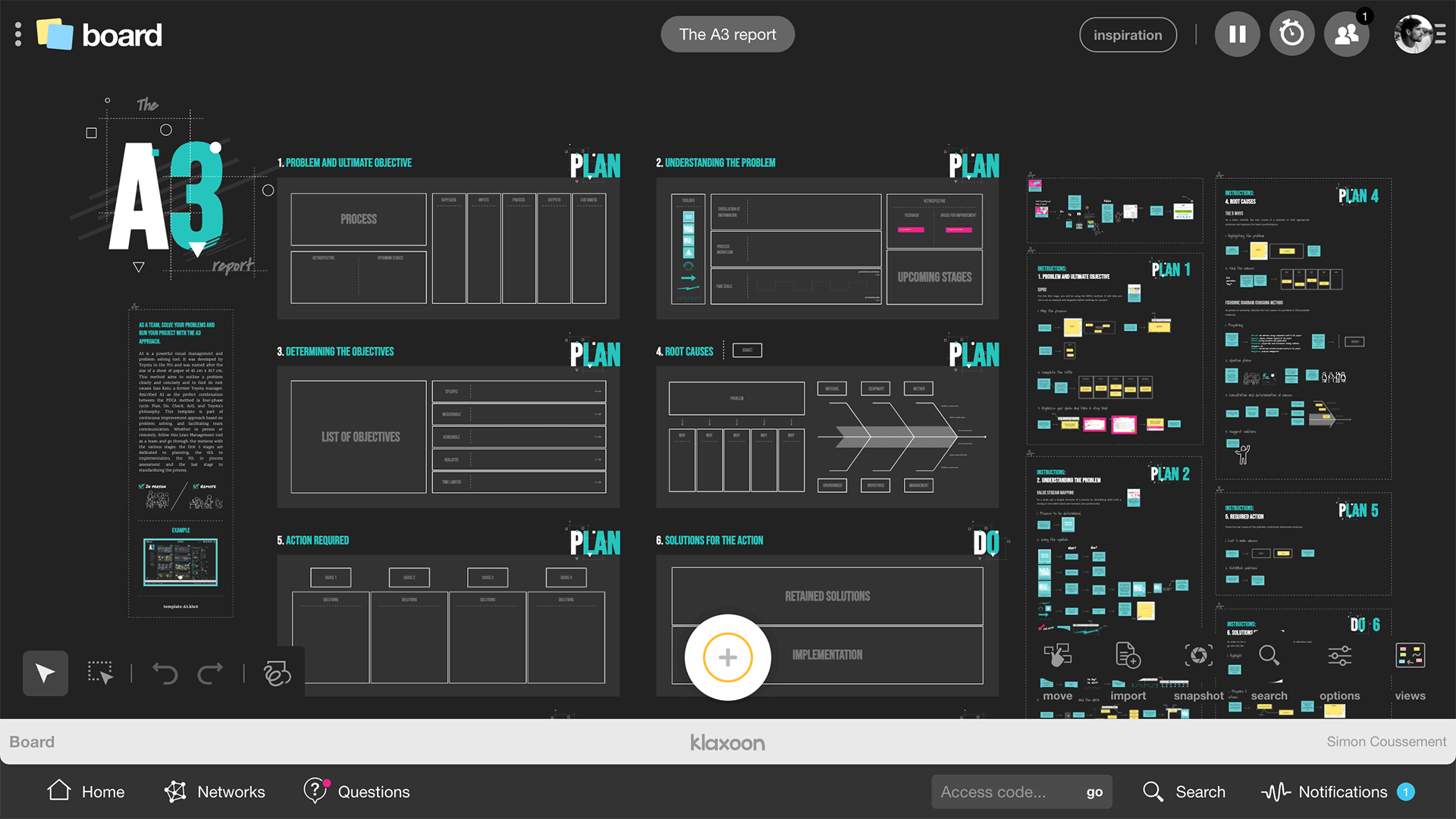
First, as it is available at any time, both on site and remotely: Board Hybrid eliminates all time and space-related constraints for users. If all or some of your team members can’t be there in person to prepare the A3 report, they can communicate via Live, the built-in videoconferencing tool. A team member who wants to host the meeting can select the “follow me” syncing tool so that other members can instantly see the areas of the Whiteboard on which the facilitator is focusing.
When working in groups with Board Hybrid, everyone can help with the preparation of the A3 report and input their own ideas (text, image or video), using colored labels. From the first stage onwards (SIPOC), highlight the most relevant ideas by asking your team to use the “Like” button (shown by a heart symbol). You can then move and sort ideas in the template matrices, and connect them using the connectors in the graphics palette.
During some of the stages, you’ll need to take decisions based on the suggested ideas. Use the “Question” tool to suggest a poll to put it to a vote: simple and efficient!
At stage 4 you identify the root causes of a problem, using the Ishikawa method (similar to the Fishbone template). Nothing better than an ideation phase with a twist - a countdown with the Timer feature - to get ideas flowing!
Finally, at stage 8, color your ideas according to the required action.
Ready to submit your A3 report? No need to send it by fax like in the old days! Just share the login code or link to the Board. And if necessary, you can download all the collected data in a .csv file. Our ready-to-use-template gives you a comprehensive framework to work on the A3 report method. You can even make any adjustments you want, according to your specific requirements. Now it’s over to you!
You too can adopt Klaxoon!
With Templates, innovate in the management of your projects, represent them visually and move forward as a team in a synchronized manner